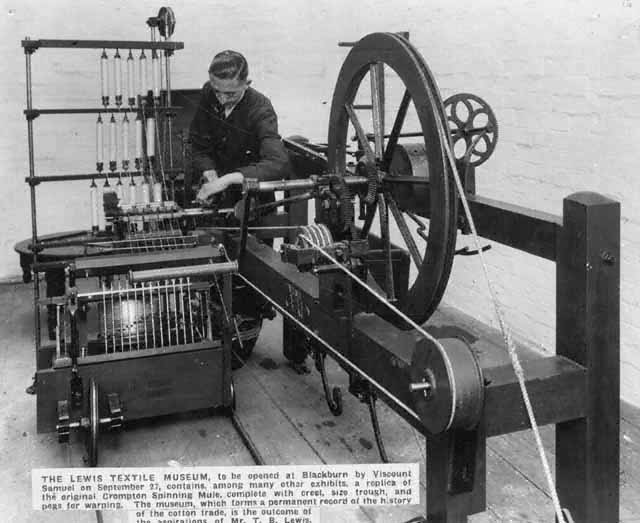
The spinning jenny represented an advance in spinning capability, but was still hand operated and machines of 30 spindles were the largest ever made. It was the introduction of the mule and the water frame that dramatically improved productivity. By the mid 1820s a power assisted mule with 600 spindles could process 100 pounds of cotton in as little as 135 hours. Further improvements to the mule during the early 19th century increased not only its speed, but the quality of the finished thread, making it strong enough to be used as a warp, enabling all cotton cloths to be woven.
The adoption of powered machinery in weaving developed at a slower rate. Edmund Cartwright's loom of the early 1780s was not successful. William Horrocks introduced an improved loom in 1803, which had a more effective means of winding the woven cloth on to a beam at the back of the loom. Improvements continued, and in 1841 William Kenworthy and James Bullough invented the weft-stop motion, which halted the lathe of the loom, if a shuttle was trapped in the warp, making it easier for a weaver to supervise more than one loom.
The shift from agriculture to manufacturing had already begun before industrialisation, but gained momentum as the demand for workers in the mills increased. In the days of handloom weaving work was shared among the family and small scale farming was carried out. There was a degree of flexibility in working patterns and when a piece of cloth was finished and had been sold, the weaver had the option of taking a day off, or cultivating his small plot.
The mills were more demanding. Machines didn't need a rest, machines didn't need days off, and as far as was possible employers tried to obtain the same output from their workers. Shorter hours and holidays were only grudgingly conceded.
Use of machinery brought changes in the pattern of family work. Cotton factory workers tended to be young. A survey in the Factory Commission Report of 1834 showed that 88% of workers were aged 30 or under and 61% 20 or under. Middle aged and older workers made less efficient factory workers, having poorer dexterity and eyesight.
One of the early impediments to the adoption of steam power instead of water power was the shortage of skilled labour.
The early steam engines and particularly the boilers needed very careful regulation and maintenance. It was to be some time before sufficient numbers of people had acquired the necessary skills, and entrepreneurs felt confident enough to make the switch to steam.
Early factories were scattered and often built in thinly populated parts of the country, where labour was scarce and there was an established tradition of workers leaving their looms to help with the harvest. At the time the employment of women and children in mills was considered too disruptive to family life.
Mechanisation initiated the method of production known as the factory system. Hargreaves' spinning jenny really only speeded up spinning by hand, it was the inventions of Arkwright and Crompton, which required power, that fundamentally changed things. That power was initially water, but by the 1830s steam power had superseded water.
Crompton's mule transformed the spinning process, enabling fine yarns to be produced that could compete with the output of Europe's most skilled workers, who were based in Switzerland. The successful application of steam power to the mule led to it becoming the predominant spinning system.
The bleaching process was transformed when chemicals replaced the previous system which required cloth to be tentered in open fields for weeks. The perfection of the power loom invented by the Cartwrights depended on the work of others such as Radcliffe, Horrocks and Marsland and by the 1830s there were 100,000 power looms in operation. Mills were still small, in the 1820s 100 to 200 hands was typical, but the fully evolved factory with its complementary processes had arrived.
In the second half of the 18th Century, the output of the domestic spinner could not keep pace with that of the handloom weaver. As the weavers were bound to return their completed pieces by a stated date, they often had to scour the countryside in order to get sufficient yarn. According to a contemporary account by Guest, a weaver might have to travel up to four miles in a morning in order to obtain enough weft to keep his loom occupied in the afternoon and evening.
Inventors and experimenters turned their thoughts to solving the problem of shortage of yarn. James Hargreaves who lived at Stanhill near Blackburn invented a Jenny which could spin up to 20 threads at the same time, and the number was soon increased to 60. Richard Arkwright worked in a school master's house at Preston, where he perfected a spinning frame. Local hand spinners, frightened that the new machinery would take away their occupation, rioted in 1768 and smashed up all James Hargreaves' Jennies in the Blackburn area. He moved to Nottingham, where conditions were more peaceful. Richard Arkwright, alarmed at the turn of events also moved to Nottingham where he continued to improve his machine, patenting his method of spinning by rollers in 1769.
Worked at first by horses, it was quickly realised that water power from a water wheel would be more economical, and that the power was sufficient to turn a number of machines at the same time. Thus a large building was needed to house the spinning frames, and a 'manufactory', a word quickly shortened to factory was born. Thus Arkwright pioneered the factory system.
He built a cotton spinning factory at Cromford in Derbyshire, and persuaded the people to come and work at the factory at regular hours, instead of at their own pace in their homes. This factory system was soon copied by other manufacturers.
By J. S. Miller
Arkwright himself built a mill in Lancashire at Birkacre, near Chorley, whilst any stream of water, even in remote country areas, was harnessed to provide power to turn a water wheel and thus operate a set of spinning frames. Because of this village communities began to grow around the mills, and as they were so isolated, the factory owner had to build the houses, and also provide such services as shops, as well as a Chapel.
At Blackburn, the sources of water power were the Blakewater and the Darwen, and along the banks of the two rivers were built the first cotton factories. At Lower Darwen in 1774, and at Wensley Fold, about a mile beyond the township of Blackburn on the Blakewater, in 1775. Conditions were still unsettled, and a few years after the two factories had started working, increasing alarm spread among the hand spinners, who feared that their employment would be destroyed.
There was a trade depression in 1779, and the distress caused an outbreak of rioting. On October 7th, 1779, the rioters visited Wensley Fold Mill, and threw all the machinery into the river. Lower Darwen Mill was left untouched, as the machines were smaller. The same year as the rioting, another spinning machine was invented at Bolton by Samuel Crompton, named the "Mule" because it combined the features of Arkwright's and Hargreaves' inventions. This was not adapted at first for use in factories, but used in small domestic workshops, it was able to spin a much finer thread than any other machine.
By J. S. Miller
In the mid 1780s trade revived to such an extent that the import of raw cotton into Lancashire trebled. Cotton became a fashionable material, and was worn by all ranks in society. One factor in establishing this was the improvement in printing of calicoes, a trade which had moved from London to Lancashire, and in which Blackburn played an important part. The Peels, the Claytons and the Haworths all developed and perfected the art, the Peels at Oswaldtwistle, the Claytons at Bamber Bridge, and the Haworths at Mill Hill.
Edmund Haworth was reputed to have been the first calico printer in Lancashire. In the 1780s he built a spinning mill alongside the printing works, which was a three storey building, 33 yards long, with 1788 spindles. In the same decade, the mill at Wensley Fold was rebuilt and enlarged, the new building being the largest of any of the early cotton mills, and five storeys high. Another mill was built in the centre of the town, at Spring Hill, near the Boulevard.
The early factory masters tried out a system which was half way between the domestic and the factory system. Hand powered spinning machines and handlooms were installed in a large building, so that there was more control, and the employer could ensure that the machines were used to their full capacity by working shifts.
The outbreak of war with the French in 1793 interrupted the cotton trade with Europe. This was offset to some extent by a switch to American exports, and the home market found a new outlet in printed cotton for soft furnishings and curtains.
Nevertheless, the 1790s saw the bankruptcy of two of Blackburn's cotton factories, Wensley Fold in 1795, and Mill Hill in 1799. The Haworths at Mill Hill were declared bankrupt in May in spite of owning a calico printing works as well as a spinning factory. They also owned an estate in Rossendale, with a mill which they let to tenants, and another Cotton Mill at Preston, which was let to Messrs. Newsham and Horrocks. Both the tenants became bankrupt as a result of the difficulties of the Haworths. There were three thousand pieces to dispose of at Mill Hill print works.
This shows that the cotton industry in Blackburn was worth a great deal of money by the end of the 18th century. An estimate made in 1800 puts the capital value of the cotton trade in Blackburn township alone at £4,000,000 per annum.
By J. S. Miller
In 1825, power looms were installed in Jubilee and Park Place mills, and these proving successful, other factory owners made preparations to replace their handlooms by power looms. In April 1825, the handloom weavers of Blackburn were incensed by their low wages which they regarded as being caused by the competition from power looms. They rioted, visited all the mills of Blackburn, smashing all the power looms they could find. The resulting clash with the authorities ended with three dead and five seriously injured.
The destruction of the power looms could not halt progress. In 1827 William Dickinson of Blackburn patented an improved power loom. There is a half-size working model in the College of Technology in Blackburn. The 1830s were a period of improvement in the mechanism of the loom. In Blackburn William Kenworthy worked on loom design at Hornby's mill, at Brookhouse, bringing out several patents. He was assisted in the work by James Bullough.
By this date specially constructed single-storey buildings were being erected to house power looms which earlier had been on the ground floor of the mill. These loom sheds had long rows of north facing windows in the roof, giving a saw-tooth look when viewed from the side. Some early weaving sheds in Blackburn built alongside existing spinning mills were at Brookhouse (1830), Nova Scotia (1833), and George Street West (1834), while in 1835, Furthergate Mill was built as a combined spinning will and weaving shed.
A return prepared in 1833 gives an insight into working conditions in the early factory system. Acts passed in 1818 and 1833 had restricted the hours for which young people could work, and the age at which they could start. The 1833 Act also appointed Inspectors to ensure that the terms of the Act were carried out. The 1833 return was prepared for the Factory Inspectors, and seems to relate to George Street West Mill or Feilden's Factory. There were 194 weavers, of whom only four were men. The youngest was an eleven and a half year old girl. The average weekly earnings, on piece work, of all weavers was 8s. 6d. (42 ½ p.), while the average among the twelve to thirteen year olds was 4s. 9d. (23 ½ p.). Most of the spinning was on Water Frames, or throstles, whose attendants earned 6s. 6d. (32 ½ p.) per week. There were some self-acting mules installed, and the spinners on these, all men, earned 26s. 6d. (£1. 32 ½ p.) . Their assistants, the piecers earned 5s. 6d. (27 ½ p.). Overlookers earned 25/-. (£1. 25p.) to 40/-. (£2.00) per week.
The bulk of the workforce came from Lancashire, two thirds from Blackburn or its surrounding area. Among the injuries and diseases which forced operatives to give up work, crooked knees and crooked legs were the most common. Usually, by the age of sixteen or seventeen the symptoms were so bad that young people were unable to continue work. Other causes were strokes and inflamed eyes, while one weaver, who had started work at Jubilee Mill and then transferred, had to retire from weaving with broken fingers.
Altogether, the picture is one of hard, monotonous work for little pay, and with additional risk of a premature end to a working career due to injury from machinery, or bodily deformations caused by working long hours in early life. While long working hours were prevalent in the early factories, it was not until the 1830s that agitation was started with a view of getting the hours of work reduced.
The industrialisation of the cotton industry sucked in workers like a fire sucks in air. The population of towns like Blackburn and Darwen increased threefold in the first half on the nineteenth century. With few exceptions living conditions were grim. When one worker complained to the mill owner that the houses weren't fit to live in, he was told they weren't for living in, they were for sleeping in, the mill was for living in.
The free and easy days of the handloom weaver were gone. Now lives were ruled by the factory whistle and the rattle of wires on the bedroom window as the knocker-up made his rounds.